
Ceramic Button
戦中のロストテクノロジー。有田の軍用ボタンとの出会い。
【手記】 / text by Yuko Kohga
はじめに 「ミッシングリンク」は、今後さまざまな視点で技術や文化を追いながら、探求・情報発信していきます。 このプロジェクトをはじめるにあたり、数えきれないほど多くの人や物との出会いと発見がありました。ミッシングリンクという プロジェクトを始めるに至る現在までの経緯を、プロジェクトの前段として「手記」としてここに残します。- 甲賀 ゆうこ
ロストテクノロジーとの出会い
はじまりは佐賀県の有田町で発見された「セラミックボタン」でした。 一見して何の変哲もないボタンですが、その正体は陶磁器で制作された軍服のボタン。 戦後70年以上の時を経て、有田の小学校の改修工事中に偶然土中から発見されたものでした。 そもそも有田は、文腺・慶長の役(豊臣秀吉の朝鮮征伐/1592ー1598)に参加した藩主・鍋島直茂が、帰国に際して連れ帰った朝鮮の陶工・李参平(り・さんぺい)によって開かれた窯業の町。「有田焼」の名は、名工柿右衛門をはじめとする歴史ある窯と共に古くから知られています。
有田にある小学校の新築工事中に偶然発見された軍服ボタン。
どれを見ても精巧な作りで、長年経った今でも圧倒的な強度を誇る。有田歴史民俗資料館蔵
そうした有田では、かつて陶磁器のボタンをはじめ、貨幣や兵器などが陶磁器で製造されていました。そのきっかけは太平洋戦争。戦争の激化とともに国内では兵器の原料となる金属が大量に必要とされるようになりましたが、資源を輸入するのが困難になったことから、日常生活で使う金属も不足します。
そこで、金属の代わりとして焼物の陶製による代用品の生産が行われたのです。有田は佐世保の海軍基地が地理的に近いこともあり、軍の意向により代用品が内密に作られるようになります。そうした背景から、伝統工芸で培った高度な技術を用いて実現したひとつが「有田焼のボタン」だったのです。
戦前は有田焼の産地として産業を確立していましたが、戦時中は贅沢品としての工芸産業は一時期ストップせざるを得ない状況に。名工たちは軍の用命により、この軍用ボタンをはじめ、「陶銭」と呼ばれる陶器でできたお金や手榴弾、つぼ詰、地雷、果てはピストルの銃身までを作っていたといわれています。
終戦によりこうした代用品は進駐軍が来る前に、すべて廃棄処分とすることが命令され、土中に埋められたり、処分されました。そのため、それぞれの詳細が記録されることもなく、ついに陽の目を見ることなく人びとの記憶から消えてゆくこととなりました。
土中から姿を現した「セラミックボタン」との対面は、静かな山間にある焼き物の町・有田に戦争の波が寄せた痕跡であり、記録されることのなかった知られざる”有田の死角”が歴史のなかにあることを知った瞬間でした。
これは一輪挿しではなく、なんと陶磁器製の“手榴弾”。陶磁器製の手榴弾は頑丈すぎて不発弾が多かったそう。撮影場所:藤巻製陶所にて
発掘場所である旧有田小学校跡地 資料:有田歴史民俗資料館
有田で製作されていたが、終戦に伴い発行されることのなかった幻の「陶銭」。
出典引用元:『爆弾から貨幣まで(昭和41年10月発行)』
発掘されたもののなかには、手榴弾の姿も 資料:有田歴史民俗資料館
写真右:超絶技巧を持つ職人・清水時一氏の手で、軍事需要品(爆弾)などが製作されたという 写真左:兵器のサイズと設計図。出典引用元:『爆弾から貨幣まで(昭和41年10月発行)』
はじめてボタンを手にした瞬間。割って中身が陶磁器かを確かめる。撮影場所:竹重クラフトタイルにて
さまざまな偶然が重なり、有田を訪れていた私が出会うことのできた「セラミックボタン」ですが、はじめて手にしたときに感じたのはプラスチック樹脂と見違えるほどの軽さ、そして、まったく狂いのない形状の精巧さでした。まるで陶磁器とは思えないほどの完成度です。
現在のプラスチック製工業ボタンでは当たり前の形状ですが、70年以上前の製法であるにもかかわらず割れ物とは思えないほどの強度を持つ4つ穴ボタンで、個体差が全くなく、緻密な技巧の品へと仕上がっているのです。
「戦時中にもかかわらず、ここまで高度な技術を確立していたなんて本当に信じられない……」
精巧な4つ穴ボタンを手にしたとき、寸分の狂いも無いものを作り出すことのできる当時の技術力に驚くとともに、知られざる“空白の歴史”への好奇心と、考古学的にも重要な遺物を発見したのではなかという胸の高鳴りを覚えました。
「何としても、この知られざる驚異的な技術を再現したい。どうにかして現代に復刻させることはできないのだろうか」と、「セラミックボタン」復刻のために私たちは動きはじめました。
現物と戦時中の記録を見比べながら検証を行う。撮影場所:有田歴史民俗資料館にて
窯業試験場や名古屋の工業セラミックを製作している企業を訪れ、製造方法のヒントを探る
復刻計画の始動からほどなくして、私たちはとても高い壁にぶつかります。現在のテクノロジーがあれば容易に再現できるはずだという考えがそもそも甘く、いざ制作方法を求めて試験場や工場を巡ったところ、出てくる答えはすべて「素材や製法が不明」。ゆえに“再現不可能”という厳しい現実を突きつけられたのでした。
「人類が月に行く時代なのに、70年以上前のボタンが再現できない……!?」
現代の先進技術や職人の技を持ってしても、セラミックボタンを復刻することができないという現実は、同時に「私たちは便利になっていく世の中で“大切な何か”を失ってきたのでは?」という気づきをもたらした瞬間でもありました。
知見を求めさまざまな研究機関や職人に話を聞いて回るも、その答えは「製法がわからない」のみ。有力なヒントが得られないまま、もはや独自に調査を進めるしかないと、東京、佐賀・有田、金沢、瀬戸と、陶磁器の欠片を一つひとつ拾い集めるように全国の職人の元を訪ね歩きました。
製法を求めて、名古屋のアルミナ(工業用セラミック)工場を訪問
その後、科学的な側面からも分析が必要であると考え、東京工業大学の研究室とも連携。その土地にある陶石を成分分析したり、原料となる素材がどこの土地から採取されたものなのかを突き止めたり、3Dスキャナーで形を分析したりと、現代の最先端のテクノロジーの力を借りながら実験と検証を重ねます。
特に再現が難しかったのは、ボタンに“4つの穴を均等にあける”ことでした。
粘土状の陶土を石膏型で製作するのですが、焼成前は素地が柔らかく、穴を開けると穴の部分から潰れてしまいます。また、手作業で無理やり穴をあけようとすると、柔らかい粘土状の素地には均等な間隔で穴をあけることができず、ましてや1mmにも満たない精巧な間隔で4つの穴をあけることは到底不可能なことであることが判明したのです。
仮に数十個にひとつ、きれいに穴があいたとしても、高温で焼成すると穴から亀裂が入って割れてしまい、まったく使い物になりません。
さらに、工業製品のボタン形状の再現も非常に困難を極めます。石膏型を使用すると、小さなボタンは型から出すときに角が潰れてしまい、個体差のない均等で精巧な形を複数個再現することはできませんでした。
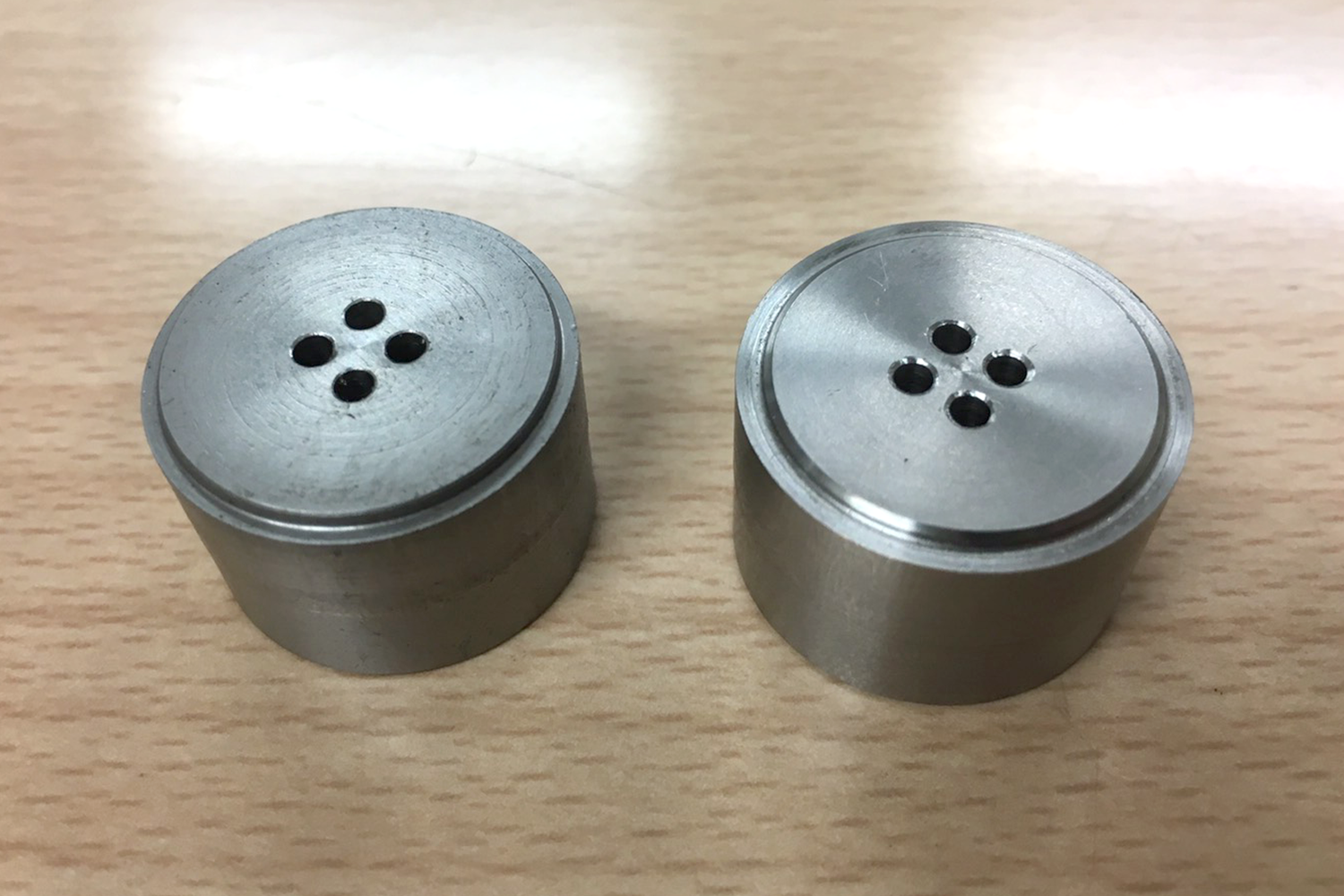
試作段階の金型
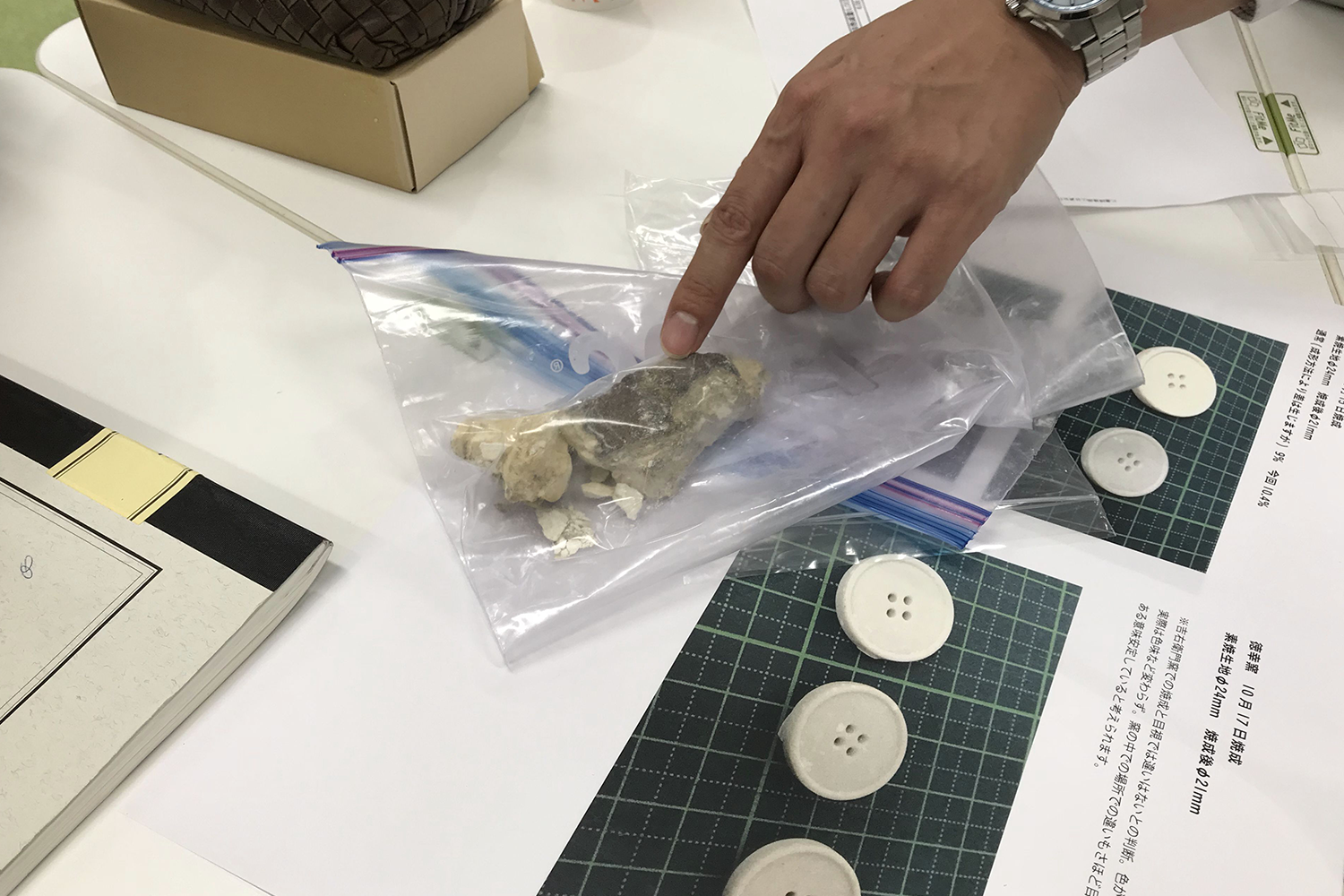
科学分析中の陶石
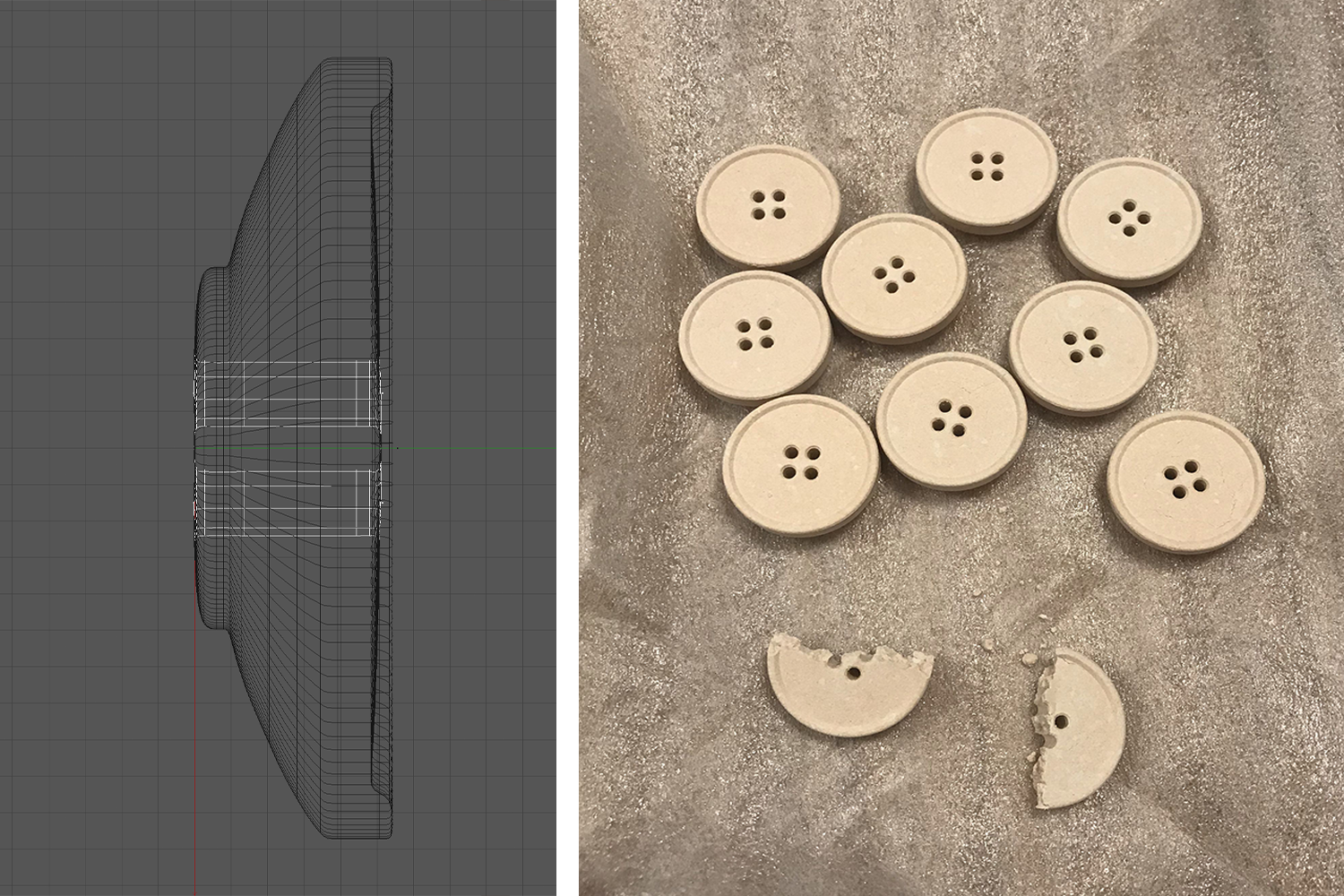
3Dレンダリングと試作段階で割れてしまった素地
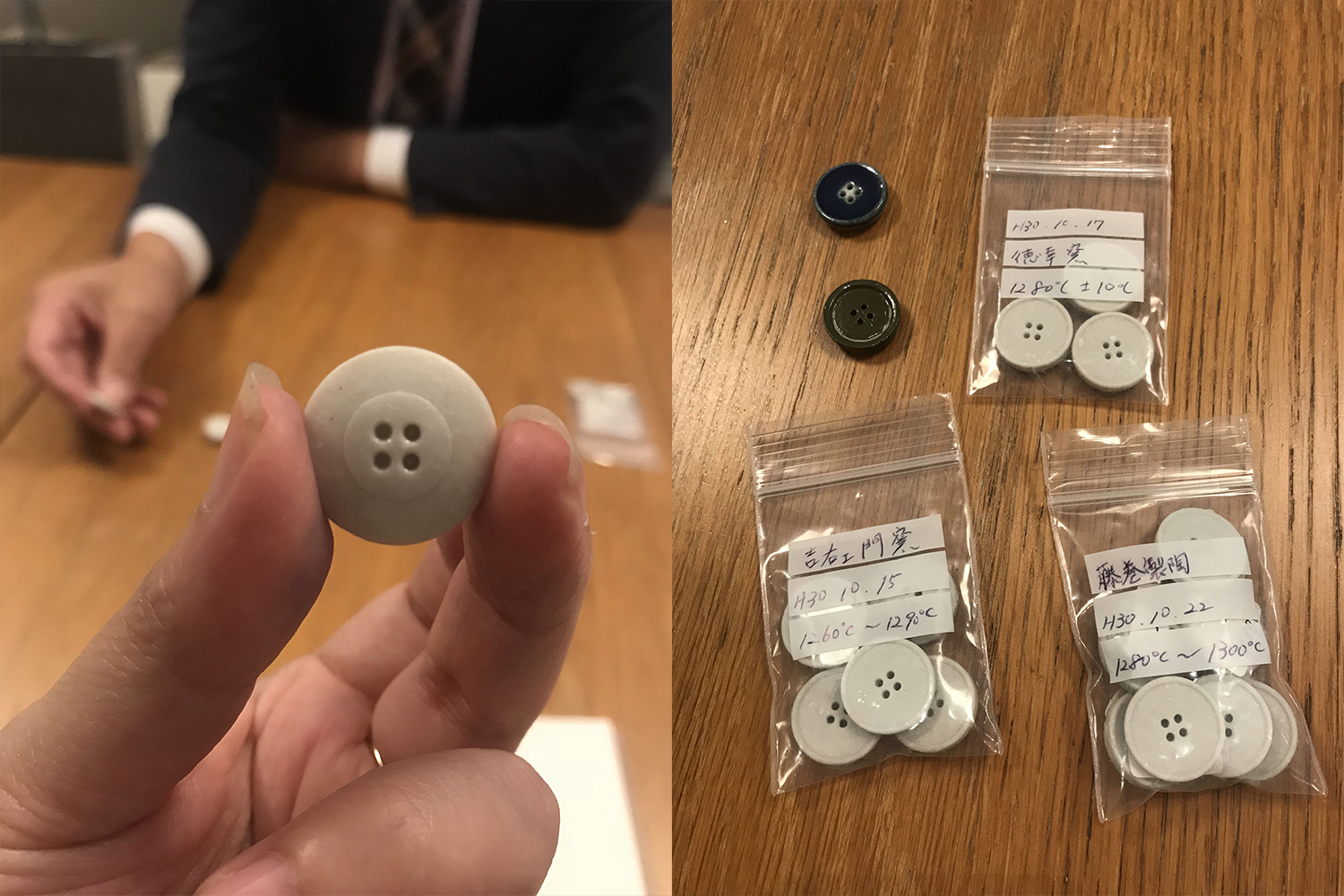
試作を重ねてできたプロトタイプ
私たちがリサーチを行なっていた当時、戦時中に軍用のボタンを作っていた「竹重クラフトタイル」三代目・竹重雅文社長は、父竹重米雄氏が磁器のボタンをつくることになった経緯について次のように語ります。
「当時の製法は不明ですが、昔は火鉢などの大物磁器を制作していました。戦前から戦中にかけて、ボタン、陶貨と順に制作を手がけるようになりました。ボタンを見るかぎり、金型によるプレス成型だったのではと推測されます。1日に1万個以上のペースで製造していたと聞いており、使用する機械は金型となれば、おそらく名古屋あたりから取り寄せていたのかもしれないですね。自社で近場に原料設備を持っていたので、泉山の原料を中心にある程度精製したものを材料として、専用にブレンドしていた可能性もあります」
竹重氏の当時の貴重な証言を元に、私たちは金型を製作。新たな成形方法で試行錯誤を幾度となく重ねました。
有田の職人の技術、商社の知見、東工大研究室の科学的側面を掛け合わせてプロトタイプの制作を繰り返すことにより、強度のある陶磁器の製法を生み出すことにも成功し、当時のボタンの製法も解明。そして、完全なる「セラミックボタン」の復刻に成功しました。
“4つの穴をあける”。たったそれだけのことですが、当時の職人が生み出した妙技を実現するには、先進の技術をもって試行錯誤を重ねても容易に再現することはできません。70年以上の空白を埋めるのは、とても困難なことでした。
「竹重クラフトタイル」二代目・竹重米雄氏。ボタンや陶銭を製作していたが、詳しい製作方法などについては多くは語らず、謎のままとなってしまった。出典引用元:『爆弾から貨幣まで(昭和41年10月発行)』
肥前窯業地区(九州エリア)で唯一のタイル製作工場「竹重クラフトタイル」三代目・竹重雅文社長。東京駅などの建材も製作を手掛けている
「ボタンといえば金属や貝でつくられるのが一般的だったなか、磁器でつくられるようになったのは戦時中の代用品だったんでしょう。(国から)要請があったのか、工場が自発的に取り組んだのかはわかりません。けれども、当時の職人はお国のためにとつくっていたんでしょうね。使う人の生活を支えるために、一つひとつ手をかけてつくっていったわけですから。想いをもってつくったからこそ、今まで残っていたのだと思います(竹重雅文氏)」
「このボタンは当時の職人のプライドと、限界まで挑戦してきた努力の結晶。だからこそ、時代を超えてずっと残っていたのかもしれない……」。竹重氏の話を聞きながら私たちは、当時の作り手に敬意を表するしかありませんでした。
有田焼の絵師(中島瞳氏)によって緻密に描かれたプロトタイプ。そのサイズわずか1cmほど
製法を再現したボタンの素地に上絵付をしたイメージ
世の中のテクノロジーが発達し、より便利な世の中になったのに、小さなボタンすら簡単に作れなくなっているのは一体なぜなのでしょう。私たちは便利がゆえに、先人から受け継いできたもの、記憶や技術的なものをどこかへ置いてきてしまったのでは。合理的で効率をはかる現代の風潮のなかで、大事な何かを過去に忘れてきてしまってるような気がしてなりません。
「セラミックボタン」の復刻を通じて突きつけられた現状に、私たちは愕然としました。
「この国には私たちが忘れてきた、多くのものや技術、そして先人たちの知恵が埋もれてしまっているのでは」。
この気づきこそがロストテクノロジーとの出会いであり、「ミッシングリンク」発足の種火となりました。
この研究により開発された技術は、今後プロダクトに応用されることを目標として、
技術発表を前提に現在もプロジェクトを続行中です(2022年現在)。
企業目線でどのような技術が求められているか
(素材)
土中から発見された当時の「セラミックボタン」は現在でも製品として使用できるほどの強度を持っており、その素材の成分分析からはじまりました。成分分析の結果「天草陶土」だということが判明しましたが、現在の産地課題として上質な天草陶土を入手することが昔に比べて非常に困難な実情が挙げられます。現在、全国の産地が一挙に天草陶土での生産に依存するなかで、本陶土による生産は今後長くは続かないと推測されます。
そこで今後は天草や他の陶土に変わり、素地の白さ、そして製品としての強度を兼ね備える新たな土(素地)の開発が必要とされます。
また、昨今のプラスチック製のボタンは、有機溶剤により国内での生産が難しいという実情もあります。これから先に向けて、製品生産(特に服飾用の製品)を考案するにあたり、日本が得意分野として培ってきた陶磁器技術をベースとした“サステナブルな素材”を原料とした服飾パーツである「セラミックボタン」こそが、次世代に求められるものとして十分に可能性があると考えられます。
(製造方法)
当時の「セラミックボタン」の製造は、金型成形によるものだと判明しました。その技術は現在、肥前窯業地区では誰ひとりとして後継者はおらず、復元できる窯元や工場は全て無くなっています。工業用セラミック以外であれば瀬戸に数件、陶磁器で工業用部品を製造している企業が存在しますが、プレス機の金型自体をつくることのできる職人がいなくなったため、現在の金型が故障などの理由で稼働できなくなると、その技術すら失われてしまうという危機に直面しています。金型においては今後、製造に影響しない新たな代替技法が必要と考えます。
また、この復刻製造過程においても、プロトタイプの制作において大いなるコストと時間、人件費がかけられおり、こうした課題は工場のラインの確保、人の確保、金型の製造の時間、図面の修正の時間など、全ての工程に起因します。これらの事項は全て生産者と制作企業が抱える問題でもあり、今後は課題をクリアする方法を率先的に導入していくことも必要だと考えられます。
産地が互いに技術協力しながら素材などの研究を進め、具体的な技術化をできるように整備することも重要であると同時に、今後は 3D プリンター出力による制作、焼成、絵付けまでの新たな陶磁器における機械の導入も必要だと考えます。このプロジェクトの製造過程においても、掘り起されて発見された70年以上前の「セラミックボタン」を完全復刻するため、3D スキャナーにてボタンをスキャンし設計しました。
(絵付けや転写方法)
人の手に依存する生産では数に限りがあり、転写でも個体差が出てしまうなど、製造における課題は枚挙にいとまがありません。バリエーションなどの展開においても、3Dプリンターにおける彫塑やインクジェットに対応する釉薬の開発、絵付けの技術導入といった多角的な検討が必要だと考えられます。